In the production of acoustic panels, laser microperforation has introduced a decisive innovation in the fields of acoustics and interior design. Compared to technologies such as punching, CO2 laser offers specific advantages in terms of efficiency, cost and quality of the final processing that open up new production possibilities. This is why more and more companies have chosen a laser machine for the micro-drilling of wood panels intended for furnishing environments such as theatres, cinemas and public or domestic premises. But what exactly are the advantages of laser in microperforation?
How CO2 laser microperforation works
CO2 laser microperforation uses a high precision laser beam to create extremely small and even holes on the surface of the material. This process is based on a non-contact technology, where the laser beam vaporizes a minimum amount of material to form the desired hole.
Thanks to the digital control capability of the laser, it is possible to customize with extreme precision the density, diameter and arrangement of the holes, adapting them to the acoustic and aesthetic requirements specific to the panel. The most popular aspects of laser microperforation include:
- Absolute hole accuracy: each hole is created with precision beyond the millimetre, ensuring smooth edges, even holes and optimum sound absorption performance.
- Infinite design possibilities: thanks to the software control of the machining and the versatility of the high definition laser, you can achieve endless patterns and extremely accurate drawings.
- Combination of functionality and aesthetics: in addition to the possibility of creating graphic effects with a practically impalpable texture, the laser-made micro-holes guarantee better sound absorption because they are more precise and homogeneous.
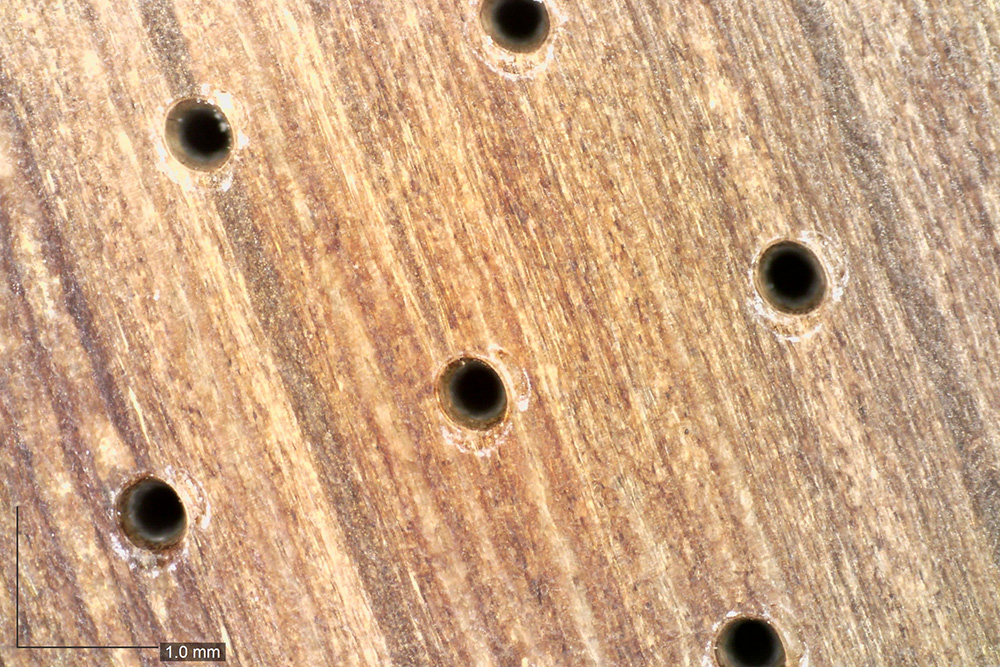
All the advantages of laser microperforation on acoustic panels
The innovation of CO2 laser for the micro-drilling of panels has allowed to improve both the production efficiency and the quality of the finished product. For companies that invest in a laser machine this means taking advantage of a number of benefits, such as:
1. Cost and time savings:
CO2 laser significantly reduces operating costs compared to traditional technologies such as punching machines. Laser microperforation allows:
- Eliminate the setup time normally required to set up or replace mechanical tools;
- Save on consumable tools, as there are no punches or molds to replace, resulting in lower maintenance and consumables costs.
2. Superior acoustic performance
As we have seen, laser microperforation allows to obtain panels with an improved sound absorption, thanks to:
- Smaller, denser holes with diameters of less than 0,5 mm, which allow for higher drilling density, improving acoustic properties and reducing noise more effectively;
- Uniform hole distribution, which optimises sound absorption.
3. Less environmental impact
The laser microperforation process is more sustainable than traditional punching. Using laser in processing:
- Waste is reduced, thanks to the precision of the laser beam which avoids waste of material;
- Waste disposal is reduced, as unlike punching, which produces residues or chips, the laser vaporizes the material, eliminating almost completely the need for disposal.
4. Reduced maintenance
CO2 laser machines require less maintenance than punching machines. In fact, since there is no mechanical contact, there are no tools that wear out. Periodic maintenance is therefore simpler and faster, reducing machine downtime and improving overall operation.
5. Customisation and flexibility
With the CO2 laser, it is possible to respond quickly to specific market demands, as it allows:
- Rapid prototyping, thanks to the possibility of changing the design of the holes in real time without additional costs.
- Adaptability to materials, as the laser can punch through materials of different hardness and thickness without requiring hardware modifications.
OT-LAS acoustic panel laser machines: Made in Italy technology for 40 years
OT-LAS is a reference point in the field of CO2 laser machines, with over 40 years’ experience and cutting-edge solutions completely Made in Italy. The commitment to quality and innovation has allowed the company to become a trusted partner for customers worldwide, ensuring partners a competitive advantage in the market. For microperforation of acoustic panels, OT-LAS laser systems offer companies:
- Innovative and proprietary technology: OT-LAS machines are equipped with advanced control systems and high precision lasers that guarantee speed in processing and high profile results.
- Reliability and durability of the machines: the quality of the systems, completely manufactured in-house, ensures optimal performance even after years of intensive use.
- Customized technical support: OT-LAS offers a complete customer service, from the installation phase to scheduled maintenance, up to custom configurations for the customer.
- Production flexibility: laser engraving and micro-drilling solutions are designed to adapt to different production needs, ensuring excellent results on a wide range of materials.
Contact us to find out about the laser system for micro-perforation tailored to your company.