In the interior design world, micro drilling of laminates so as to reduce noise in crowded spaces is an increasingly popular trend. In-depths studies in this sector prove how effective this technique is for sound insulation in indoor places. What is the special technology to be used so as to perform a pattern of identical micro holes that may be aesthetically pleasing while not damaging laminates?
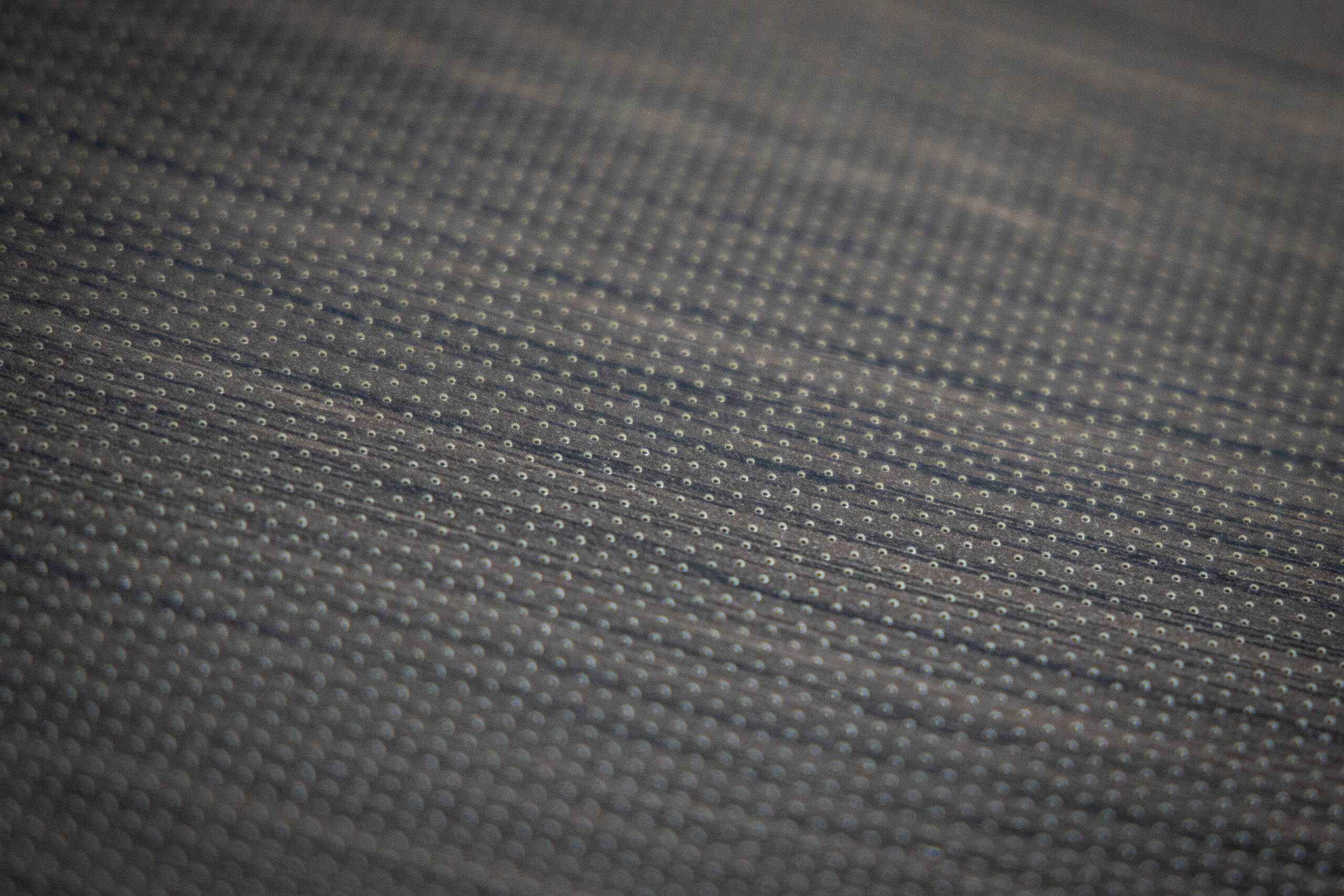
Ot-las laser technology: very-high performance hardware and software.
The radiofrequency CO2 laser is the only application able to create this type of panels. The accuracy of the beam and the contactless processing allow carrying out holes that are exactly the same and in a pre-established size, without breaking or gathering the laminate surface. An unparalleled result that could not be reached by any mechanical processing, in terms of sophistication and accuracy as well as time and cost optimization.
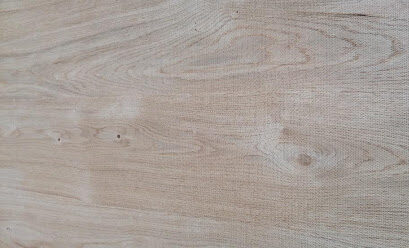
Ot-las expertise and know-how in the laser machine creation have allowed the organization to implement micro-perforation by cutting-edge technology. In order to get excellent performance, Ot-las has developed the application – from a hardware point of view – by building a table that can reach typical sizes of 3100x1300mm, without limiting itself to these. Furthermore, a special software has been devised to laser process holes and, in co-operation with EL.EN, a RF899 laser that better meets the requirements of this type of processing. This results in a unique machine, equipped with an innovative software and proper tools for micro-perforation , in combination with large-sized hardware that can guarantee the utmost accuracy in motion. That is the best laser technology for uncompromised quality.